Dorset Buttons
- Suzanne Munroe
- Feb 9, 2021
- 10 min read
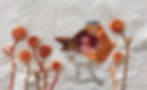
Hand stitched, pieced birdie, showcasing some of my handmade Dorset buttons
Dorset buttons are essentially covered rings. The rings can be wood, metal, or plastic, and they’re covered with thread using a buttonhole stitch
HISTORY
The Dorset Button industry flourished for 160 years employing, by the 1780s, 4,000 women and children until the button making machine was invented in 1860.
Thirty-Year-War soldier Abraham Case invented a revolutionary thread-covered button around 1622. Case’s creations were designed from locally sourced linen thread that was deftly wrapped over hand cut horn rings taken from the abundant sheep population. Making buttons provided much needed income for many in the towns and villages of Dorset, England, from the 1600s to the 1800s.
Later, in the mid-1700s, Abraham’s grandson Peter Case invented a non-rusting metal alloy that was used as a foundation for wire button rings. The wire rings gave a great boost to the already economically significant Dorset button industry. Their manufacture was at a peak between 1622 and 1850, after which they were overtaken by machine-made buttons from factories in the developing industries of Birmingham and other growing cities
Although the first button was the conical high-top, which was used primarily for men’s waistcoats, the Dorset Cartwheel, which is formed over a ring foundation, is the most recognizable.

TYPES of Dorset Buttons:
1. High Tops and Dorset Knobs: made with sheep’s horn, fabric and thread. Dorset Knobs are made on a firm disc padded with pasted fabric then put in a mould to dry then embroidered with fine thread.
2. Birdseyes and Mites, made with just fabric and thread.
Wire rings were introduced in the 1730’s and two further types of buttons were added to the range:
3. Singletons: made with wire, fabric and thread
4. Dorset Cartwheel and Blandford Crosswheel: made with wire and thread
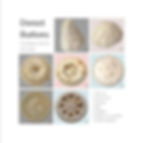
TECHNIQUES - traditional steps:
Casting (covering the ring with blanket stitches)
Slicking (turning the cast “bumps” to the inside of the ring)
Laying (wrapping thread spokes)
Rounding (filling in the spokes)—form the basis for many regional and contemporary variations.four different types of Dorset Buttons with many variations within each type.
During the early 1800s unemployment in Dorset was high, especially amongst the agricultural workforce. The average farm labourer was one of the poorest paid in the country. The combination of lack of work, poor pay and the demise of the Button Industry resulted in many families emigrating to America and Australia. Assisted emigration schemes were set up by individuals, charities and local communities to finance families wishing to start a new life overseas.
Buttoners were no longer needed and the skill of buttony was in threat of being lost. By the middle of the 1850’s, many had moved to alternative occupations such as needlewomen and glovers.
In the early 1900s, Florence, the Dowager Lady Lees, was responsible for saving the art of making Dorset Buttons. She visited farms and cottages all over Dorset to discover how these buttons were made and sought to revive the industry at Lytchett Minster. She set up a small business specializing in the production of “Parliamentary” buttons for Dorset MPs in their respective constituency colors. In 1908, these buttons were in full production. This revival was brought to an end by the outbreak of the First World War.
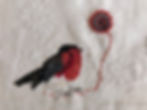
I made this Dorset Button with embroidery thread to match my birdie
Today, Dorset Buttons are a heritage craft and the skill of buttony continues. Many people still make these thread and fabric buttons for their own enjoyment. Artists are now using the technique of buttony in their works of art, generating new interest in the industry, and consequently in the lives of the original craftspeople who made them.

Replica of English smock with Dorset buttons (pinterest photo)
RESOURCES
——————————————————————————————
FURTHER READING:
From the Newsletter for the Friends of Lyme Regis Philpot Museum
HISTORY AND ART OF DORSET BUTTONS
In the first of a two part article, museum volunteer Lizzie Wiscombe gives an account of the fascinating subject of ‘Buttony’.
As a proud woman of Dorsetshire I have always had a great interest in anything uniquely Dorset. The exquisite craft of Dorset buttons, or to give it its local name of 'Buttony' is one that involved many women and children, in mainly the East of Dorset.
I was first introduced to the Dorset button at the age of 12 on the occasion of the Queen's Silver Jubilee, in 1977. The Girl Guides of Dorset were to take the ferry from Weymouth and visit Guernsey for the day. Groups of Guides, from each town, were to make their own coloured button. Lyme's group made a wonderful lilac 'Blandford Cartwheel', proudly worn on our uniform lapel. I wanted to know more.
THE HISTORY Buttons before the middle of the 19th century, prior to the industrial revolution, were made by hand. The earliest ones were hewn from bone, wood, stones, berries, shell, clay and thread (1).
Why in Dorset? The home industry began in 1622, when Abraham Case married a girl from a military family and settled in Shaftesbury. During his time as a soldier he had become interested in the work of the Northern French and Belgian button makers, who provided the metal buttons for military uniforms. A different pattern for each regiment. The county of Dorset was the perfect place to begin the production of handmade buttons. At that time it was mainly a sheep farming community, with spinning and weaving crafts as a byproduct. The raw materials and incentive were there for the production of buttons (2).
HIGH TOP BUTTON Case's first design was the High Top button, a conical shape made by shaping a piece of sheep horn, covered by cloth and then covered by tiny linen thread stitches. Makers were paid per button made. The higher the quality, the higher the payment. The women and children of a family were usually involved, working by the poor light of tallow tapers and a glass sphere, to try to magnify the light (2).
Sometimes the men helped if the deadline of 'Button Day' was fast approaching and the number of buttons produced had not been met. The author Tracy Chevalier, in her book Burning Bright (2007), has the protagonist's sister, Maisie, making money from 'Buttony'. She claimed to have 'once made fifty-four Blandford Cartwheels in one day, a record from the Piddle Valley - though a girl to the east in Whitchurch was known to make a gross [144] of buttons a day, as Mr. Case, the button agent who came monthly to Piddletrenthide, often reminded the women’. Although Maisie says later that the girl must have made simpler designs than her Cartwheels to be able to produce such a number!
In 1656 Case had to move to bigger premises, in Shaftesbury, as the popularity of his buttons grew. There were other depots in Bere Regis, Milborne St Andrew, Sherborne, Poole, Langdon Maltravers and Tarrant Keyston. All depots were visited by an agent on a particular day each week, when out-workers would bring their products for determination of quality and payment. They would then take new supplies of raw materials and return again the following week. The workers may have walked more than ten miles to attend 'Button Day'. This was rather like an open air market (3) where local women could gather and buy locally produced products, such as butter and cream and catch up on gossip!
By 1793 Shaftesbury had 4,000 women and children in the trade. Until 1800 the firm paid their workers in goods instead of cash (4). Buttony was better paid than farm labouring. At harvest time there was often conflict within the family. Women and children were needed for the harvest, so Buttony had to be done in the early morning or late into the evening, when all the farm work was completed (4).
During the first three or four weeks the children were not paid, for they 'spoilt much thread', there afterwards they were paid a penny a day for two months and then one shilling a week. Expert workers could make up to 144 (a gross) a day and, if properly done, the sum of 3/6 a gross was paid.
Prices in the 19th century ranged from 8d to 3/- a dozen for cloth covered buttons, wire ranged from 1/6 to 4/- per gross (5d for seconds) (3).
Children were also employed at the depots at Shaftesbury and Bere Regis to prepare the raw materials ready for collection. The wires or rings were made from rustproof wire, brought from Birmingham by bullock and cart (3). The wire was burned and twisted on a spindle, the nipped ends put together and soldered by expert children called 'Winders and Dippers' (2). 'Stringers' counted the rings and threaded them in lots of 144. The rings were used for the wheel type buttons (the 'cross wheel', 'Blandford Cartwheel' and 'Honeycomb'). Many other children prepared the thread in skeins for collection (3). Other women at the depot cleaned the finished buttons. Soiled buttons were placed in linen bags and boiled (1). They were then sorted and mounted on coloured card, denoting the quality of work. Yellow card for what we would know as 'seconds', blue card for standard quality and finally pink for only the highest quality buttons. Only the buttons on pink and blue cards were exported and the yellow 'seconds' would be sold locally (1). Standard buttons not exported were taken to London, once a month, by cart for sale around warehouses and clothing manufacturers (3).
The buttons’ fame of quality spread to London, where the High Tops were used to adorn the waist coats of the rich men at court. It is said that King Charles I wore three waist coats on the morning of his execution, in 1649, to stave off the cold. He did not want the gathering crowd to mistake his shivering from the cold for shaking in fear (2). One of those waist coats had buttons provided by Abraham Case, now preserved at Longleat House, in Hampshire (3).
SINGLETON BUTTON AND DORSET KNOB BUTTON The Singleton button was either invented by, or named from, the Singleton family. These were flat buttons made by fabric covering a metal ring (2). There is a rare black Singleton Button, made exclusively by Abraham Case's widow (between 1658 and her death in 1682) - the only coloured buttons made by the firm (1).
The flattened version of the High Top Button, called the Dorset Knob, was a further design originating in the 1850's. It is not known if it was named due to the button shape being similar to the famous Dorset biscuit or whether the button’s name changed with the innovation of the biscuit (2). Queen Victoria was known to own a dress lavishly trimmed with Dorset Knob Buttons. She also had a gown completely covered by High Top Buttons (3).
Bibliography & Sources
(1). Worth, R., 2002. Dress & Textiles. The Dovecote Press
(2). Howitt, M., (no date) The History of Handmade Buttons in Dorset. Buttons Buttons Pamphlet available from The Shaftesbury & District Society, Gold Hill Museum (All photos have been taken from this pamphlet.)
(3). Johns, T., 2012. Dorset Buttons - Hand Stitched in Dorset for over 300 Years. Natula Publications
(4). Powell, A., 2005. Facts About Shaftesbury - Dorset Buttons. Pamphlet available from The Shaftesbury & District Society, Gold Hill Museum Lizzie Wiscombe
HISTORY AND ART OF DORSET BUTTONS
In the final part of her article, museum volunteer Lizzie Wiscombe gives an account of the fascinating subject of ‘Buttony’. January 2018
She previously described High Top, Singleton and Dorset Knob buttons.
BIRD'S EYE BUTTONS The High Top and Knob are quite hard buttons, which make them unsuitable for children's and babies clothing, nightdresses and underwear. Hence the design called Bird's Eye Buttons, which consisted of stitching over either a thread or fabric base. It was this tiny button that ironically was suited to being made by children's small fingers (1).
CROSSWHEEL BUTTONS From the Bird's Eye and the Singleton, it is easy to see the evolution of the Crosswheel Button. This was the button that made Dorset famous and inspired many delicate variations. Huguenot immigrants, Protestants exiled from France who settled in North Dorset after 1685, brought their lace making skills when working with the buttons to produce the new intricate lacy designs (1). At the end of the 17th century, debates in Parliament had an effect on further developments in Dorset Buttony. Between 1685 and 1727 there was considerable national interest in the industry. Makers using different materials all tried to protect their interests. The needlework button makers wanted a Bill to prohibit the making of horn or hoof buttons on the grounds that they contained large quantities of imported materials, that they employed vast numbers of the poor who might lose their livelihood and that so many trades were involved in the production of buttons (1). The horn and hoof makers answered the application by questioning their import figures and stating that it was the 'poor people' who actually used the horn 19 and hoof buttons as they were unable to afford the more expensive thread ones (1).
THE DECLINE OF DORSET BUTTONS In 1807 the production of buttons was becoming mechanised in Birmingham, which became the centre of Britain's button manufacture (2). Buttons of metal and pasteboard could be made in large quantities and cheaply. The early machines made the buttons in two operations. First a strip of metal was fed into a power press which punched out four button blanks, including their holes, at each stroke. Then the blanks were put into 'wet' barrels containing water, steel shot and an abrasive powder. The barrel was then tumbled for hours, smoothing the edges and removing the burrs around the holes, preventing damage to the thread when attaching the button. By the Great Exhibition of 1851 at Crystal Palace, more machines had been made, including one producing linen buttons (made by Ashton) (1).
Within nine years the Dorset Button industry collapsed, causing poverty and hardship - not only to families but, in some cases, to whole villages (3). It was up to the government and the land owners to prevent a disaster. They made funds available to enable families to emigrate to Australia and Canada which already had ties with Dorset. 350 families from the Shaftesbury area were shipped out to the colonies to try to make a new life for themselves. There are still many descendants living there today (3).
The last member of the Case family, Henry, died in 1904, which finally ended the Dorset Button industry. Lady Florence Lees of Lychett Minster bought all the buttons that were left and tried to revive the craft. By referring to the elderly villagers who could remember the techniques, she reproduced the original patterns and created new designs. The Spangle Button dates from this time and has influenced the inspiration for the beaded buttons of the late 20th century (1). But, because handmade items are more expensive, the enterprise failed ending at the start of the First World War.
THE FUTURE The ways of making some types of buttons are now lost forever. But by looking at some buttons held in museums, the construction is often clear and can be copied. The mystery of the High Top was not revealed until the 1970's when Elizabeth Gilbert carefully unpicked an antique button (1). She was then able to teach the technique. Buttony is now famous across the world. There are Dorset Button makers in South Africa, Australasia, the USA, Canada and even Japan - it would be nice to think that there are enough enthusiasts to keep this 300 year old Dorset tradition alive. The Lyme Regis Museum does have a few Dorset Buttons in its collection, donated in the 1980's. A small card from the Old Button Shop recording this fact was discovered during the move of artefacts and documents as part of the recent building work.
Lizzie Wiscombe
Bibliography & Sources
(1) Howitt, M., (no date) The History of Handmade Buttons in Dorset. Buttons Buttons. Pamphlet available from The Shaftesbury & District Society, Gold Hill Museum (All photos have been taken from this pamphlet.)
(2) Johns, T., 2012. Dorset Buttons - Hand Stitched in Dorset for over 300 Years. Natula Publications
(3) Worth, R., 2002. Dress & Textiles. The Dovecote Press DOUBLE THAN
http://www.lymeregismuseum.co.uk/lrm/wp-content/uploads/2016/04/July-2017-newsletter-proof.pdf
http://www.lymeregismuseum.co.uk/lrm/wp-content/uploads/2018/01/Jan-2018-newsletter-FINAL.pdf